How can you add value to your co-products ? Effective strategies
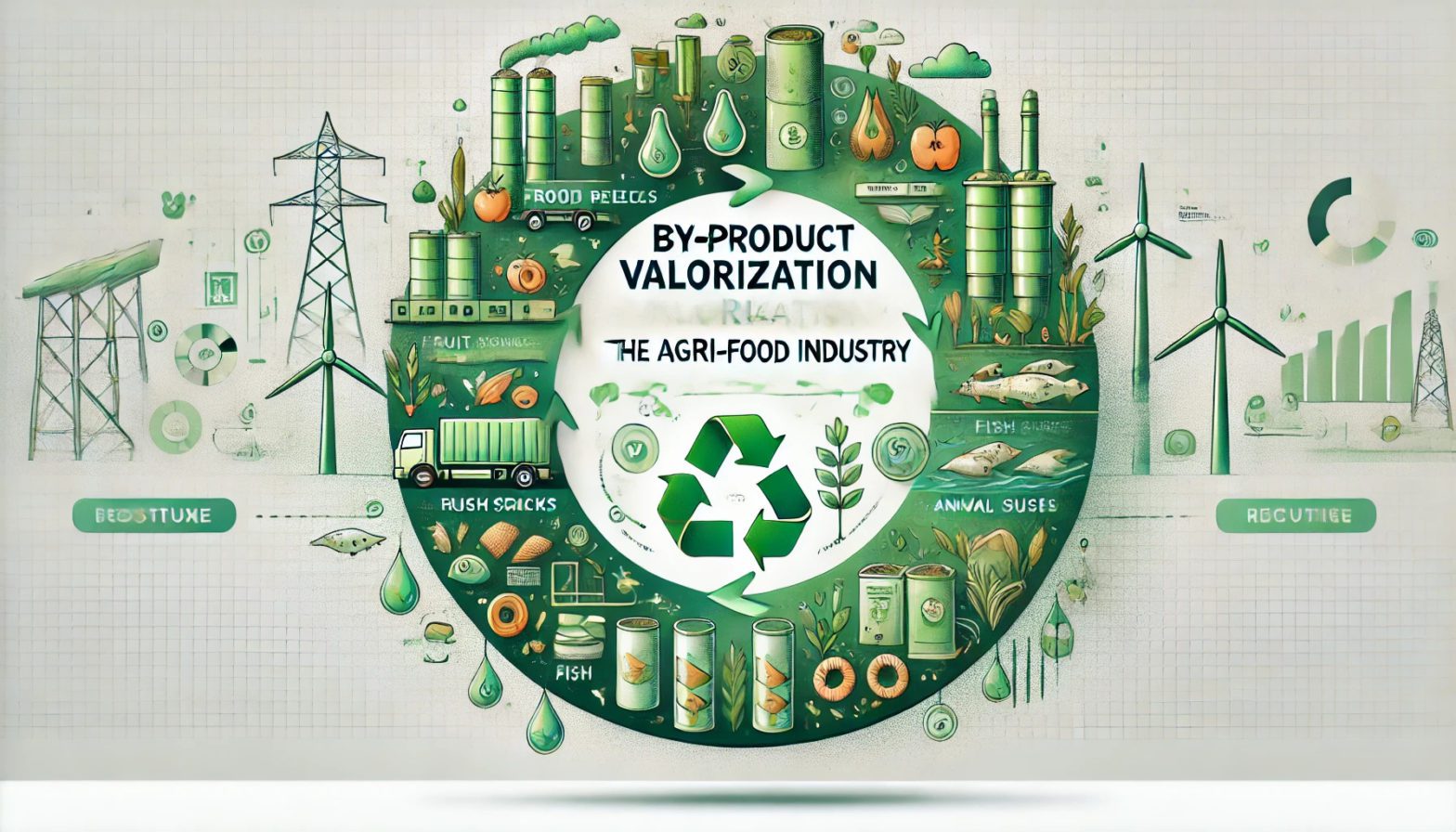
In our previous article “Waste, co-products, by-products: what are we talking about ?” we clarified the distinctions between these different terms and presented the regulatory framework that applies to them. We’re now going to look at the different strategies for adding value to these co-products, and turning them into real economic opportunities for agri-food businesses.
Every year, the French agri-food industry generates large quantities of co-products. According to the Réséda 2017 survey [1], the volume of co-products from the main agri-food industries in France was estimated at 12.1 million tonnes of Dry Matter, an increase of 2 Mt compared to the 2008 survey [2]. These materials represent both a daily management challenge and an under-exploited economic opportunity.
The hierarchy of recovery methods: a structured decision-making framework
European Directive 2008/98/EC establishes a precise hierarchy for the recovery of materials, giving priority to options that preserve their value as far as possible. This recovery pyramid provides a strategic guide for prioritizing actions by agri-food sector.
Human food: the highest economic potential
Recovery for human consumption is the most economically viable option. According to the study by Caldeira et al [3], this approach contributes directly to the reduction of food waste, a major challenge for the industry. Indeed, cereals, fruit and vegetables are identified as being responsible for the largest quantities of food waste in the European Union.
Upcyclink has developed particular expertise in this field, working in particular with Vives-Eaux, a company specializing in seafood processing. The aim of the project was to recycle 100% of the 3,000 tonnes of fish processed annually, by recovering the flesh and selling it on the pulp market to make prepared dishes such as brandade or fish balls.
Animal feed: a proven solution with a rapid ROI
Animal feed is often the first stage in a value-adding strategy, due to its relative ease of implementation and the existence of structured channels. According to the Réséda survey [1], animal feed recovers around 9.3 Mt of MS, or 76% of the tonnage of co-products generated in France [2].
As Chapoutot et al [2] point out, “from the moment a co-product is destined for animal feed, it becomes a raw material for animal feed and must comply with the relevant regulations”.
The Saumup project, run by Upcyclink in collaboration with Saumextra, is a perfect illustration of this approach. This project aims to valorize the by-products of salmon processing (skins, heads, etc.). The workshop generates 120 tonnes/year of low value-added by-products (flour). The aim is to adapt existing processes so that filleting by-products can be recycled, partly as ingredients for human consumption and partly as products for pets.
Energy and agronomic recovery: complementary alternatives
In the absence of other outlets, agri-residues can be used to produce energy via methanization or combustion. According to Réséda (2017), only 3% of the tonnage of co-products is destined for energy recovery (methanization, combustion).
Material recovery, such as transformation into natural fertilizers or biomaterials, also offers interesting solutions. According to Chapoutot et al [2], 6% of tonnage is destined for agronomic uses (land application, fertilization, composting).
Upcyclink proposes a “zero waste” approach that also integrates the valorization of by-products into plant feed, thus completing the pyramid of valorization: feeding man, then animals, and finally plants and soils.
Practical methodology for an effective value-addition strategy
To maximize the value of co-products, companies need to adopt a methodical approach that takes into account several key criteria.
Map available co-products
Before considering a value-addition solution, it is essential to accurately assess the co-products available :
- Accurately quantify the volumes of co-products generated
- Analyze their composition (proteins, fibers, lipids, micronutrients)
- Assess their stability and conservation constraints
This analysis enables the most suitable value-addition routes to be identified. As Chapoutot et al [2] point out, the chemical composition of co-products varies greatly depending on the botanical family and the technological treatments applied, and this influences their potential valorization.
Upcyclink systematically begins with a co-product audit and market studies demonstrating the project’s economic potential.
Assessing economic profitability
A recovery solution must be economically viable for the company. This involves :
- Comparing disposal costs with recovery costs
- Identifying existing markets and outlets
- Calculating short- and long-term return on investment
Upcyclink carries out technical and economic feasibility studies on selected recovery routes, enabling a sound business case to be presented for decision-making.
Integrate operational and regulatory constraints
The implementation of a recovery solution must be adapted to industrial constraints and not disrupt existing processes. Investment requirements, operational complexity and compatibility with current production are determining factors.
In addition, any recovery strategy must respect the legal framework and the expectations of stakeholders, in particular health and environmental regulations. Since January 2024, the obligation to sort bio-waste at source has applied to everyone, regardless of the volume or activity of the producer/holder, reinforcing the need for optimized management of co-products.
Taking potential health risks into account
According to Chapoutot et al[2], three types of risk need to be taken into account when adding value to co-products: biological risk (bacteria, mycotoxins), chemical risk (heavy metals, PCBs, dioxins) and physical risk.
Wet co-products, particularly from the fruit and vegetable and dairy industries, are the most sensitive to bacterial contamination. Dried or granulated co-products, on the other hand, generally have low levels of microbial contamination.
The presence of mycotoxins can be observed in certain cereal co-products, particularly corn and bioethanol co-products, which calls for particular vigilance when using them in animal feed.
Implement the new recovery process
Implementing a recovery strategy requires a gradual approach :
- Test on a small scale before rolling out on a large scale
- Train teams in the new processes
- Set up monitoring indicators to measure results
Upcyclink designs and engineers recovery facilities, and carries out pilot tests to validate the process and end products according to the specifications of identified buyers.
Références :
[1] Réséda. (2017). Gisements et valorisations des coproduits des industries agroalimentaires. Rapport d’étude.
[2]Chapoutot, P., Rouillé, B., Sauvant, D., & Renaud, B. (2019). Les coproduits de l’industrie agro-alimentaire : des aliments de qualité à ne pas négliger. INRA Productions Animales, 32(2), 167-184. https://doi.org/10.20870/productions-animales.2019.32.2.2504
[3]Caldeira, C., De Laurentiis, V., Corrado, S., van Holsteijn, F., & Sala, S. (2019). Quantification of food waste per product group along the food supply chain in the European Union: a mass flow analysis. Resources, Conservation and Recycling, 149, 479-488. https://doi.org/10.1016/j.resconrec.2019.06.011